Introduction
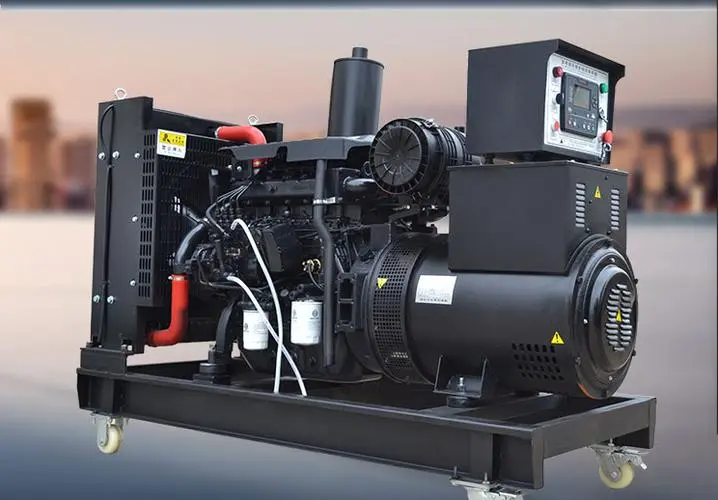
Diesel generators are crucial equipment used in various industries and settings to provide backup power during grid failures or in off-grid locations. Ensuring the reliable operation and optimal performance of diesel generators is essential for maintaining continuous power supply and preventing disruptions in critical operations. Performance monitoring plays a key role in achieving these objectives by enabling operators to track the efficiency, health, and overall condition of the generator system.
This article aims to explore the importance of performance monitoring for diesel generators, the various parameters that need to be monitored, and the technologies and tools available for effective monitoring and analysis. By implementing robust performance monitoring practices, operators can proactively identify issues, optimize maintenance schedules, and enhance the overall reliability and efficiency of their diesel generators.
Importance of Performance Monitoring for Diesel Generators
Performance monitoring of diesel generators is essential for several reasons:
1. Early Detection of Issues: Continuous monitoring of key parameters such as engine temperature, oil pressure, fuel consumption, and vibration levels can help in detecting potential issues or anomalies at an early stage. Timely identification of problems allows operators to take corrective actions before they escalate into major failures, reducing downtime and repair costs.
2. Optimal Operation: Monitoring the performance of a diesel generator allows operators to ensure that the system is operating within its design parameters and delivering the expected power output. By tracking parameters such as fuel efficiency, load capacity, and emissions levels, operators can optimize the generator's operation for maximum efficiency and reliability.
3. 300kw diesel generator for remote agricultural operations : Performance monitoring enables predictive maintenance practices by providing real-time data on the health and condition of critical components. By analyzing trends and patterns in the data, operators can anticipate maintenance needs, schedule preventive repairs, and avoid unplanned downtime.
4. Compliance and Reporting: Monitoring performance metrics is essential for ensuring compliance with regulatory requirements and industry standards. By maintaining accurate records of performance data, operators can demonstrate adherence to safety and environmental regulations, as well as track the generator's performance over time for reporting purposes.
Key Parameters to Monitor for Diesel Generators
To effectively monitor the performance of a diesel generator, operators need to track a range of key parameters that provide insights into the system's health, efficiency, and reliability. Some of the critical parameters to monitor include:
1. Engine Parameters:
- Engine speed: Monitoring the RPM of the engine can indicate the load conditions and performance of the generator.
- Engine temperature: Tracking the coolant temperature and exhaust gas temperature helps in preventing overheating and ensuring optimal engine operation.
- Oil pressure: Monitoring oil pressure levels is crucial for lubrication and preventing engine damage due to insufficient lubrication.
2. Electrical Parameters:
- Voltage and frequency: Monitoring the output voltage and frequency of the generator is essential for ensuring stable power supply to connected loads.
- Load capacity: Tracking the load on the generator helps in balancing the power demand and preventing overloading.
3. Fuel System Parameters:
- Fuel consumption: Monitoring fuel consumption rates can help in optimizing fuel efficiency and detecting leaks or inefficiencies in the fuel system.
- Fuel level: Tracking the fuel level in the tank ensures that the generator has an adequate fuel supply for uninterrupted operation.
4. Environmental Parameters:
- Emissions levels: Monitoring emissions such as NOx, CO, and particulate matter helps in compliance with environmental regulations and ensures minimal impact on air quality.
- Ambient conditions: Tracking ambient temperature and humidity levels can help in optimizing the cooling system and preventing overheating.
Technologies and Tools for Performance Monitoring
Several technologies and tools are available for performance monitoring of diesel generators, ranging from basic sensors to advanced monitoring systems. Some of the common technologies used for performance monitoring include:
1. Sensors and Instrumentation:
- Temperature sensors: Used to monitor engine temperature, coolant temperature, and exhaust gas temperature.
- Pressure sensors: Used to measure oil pressure, fuel pressure, and air pressure in the intake system.
- Vibration sensors: Used to detect abnormal vibrations in the engine and generator components.
2. Control Systems:
- Engine control modules (ECMs): Provide real-time data on engine performance, fuel consumption, and emissions levels.
- Generator control panels: Allow operators to monitor and control the generator's operation, as well as set alarms for abnormal conditions.
3. Remote Monitoring Systems:
- Telematics systems: Enable remote monitoring of generator performance through cloud-based platforms, providing real-time data and alerts to operators.
- SCADA systems: Supervisory Control and Data Acquisition systems allow centralized monitoring and control of multiple generators in a networked environment.
4. Data Analytics and Software:
- Predictive maintenance software: Utilizes data analytics and machine learning algorithms to predict equipment failures and optimize maintenance schedules.
- Performance monitoring software: Provides dashboards and visualizations of key performance metrics, enabling operators to track the generator's performance in real-time.
Best Practices for Diesel Generator Performance Monitoring
To ensure effective performance monitoring of diesel generators, operators should follow best practices that enhance reliability, efficiency, and safety. Some of the key best practices include:
1. Regular Inspections and Maintenance:
- Conduct routine inspections of the generator system to check for leaks, wear and tear, and signs of damage.
- Follow manufacturer-recommended maintenance schedules for servicing critical components such as filters, fluids, and belts.
2. Data Logging and Analysis:
- Record and store performance data from sensors and control systems for analysis and trend monitoring.
- Use data analytics tools to identify patterns, anomalies, and potential issues that require attention.
3. Alarm and Alert Systems:
- Configure alarm thresholds for key parameters to receive real-time alerts for abnormal conditions.
- Respond promptly to alarms and take corrective actions to prevent failures or shutdowns.
4. Operator Training and Awareness:
- Provide training to operators on the importance of performance monitoring and how to interpret key performance metrics.
- Foster a culture of proactive maintenance and continuous improvement to optimize the generator's performance.
Conclusion
Performance monitoring is a critical aspect of maintaining the reliability and efficiency of diesel generators in various applications. By monitoring key parameters such as engine performance, electrical output, fuel consumption, and environmental conditions, operators can proactively identify issues, optimize maintenance practices, and ensure uninterrupted power supply. Leveraging technologies such as sensors, control systems, remote monitoring platforms, and data analytics tools can enable operators to enhance the performance monitoring capabilities of their diesel generators.
By implementing best practices such as regular inspections, data analysis, alarm systems, and operator training, operators can maximize the uptime, longevity, and performance of their diesel generators. Continuous improvement in performance monitoring practices will not only reduce downtime and maintenance costs but also contribute to a more sustainable and reliable power supply infrastructure for critical operations.